
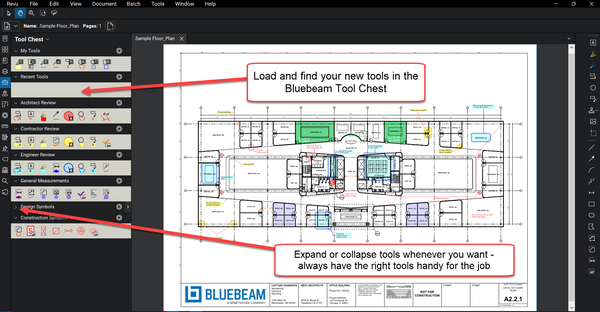
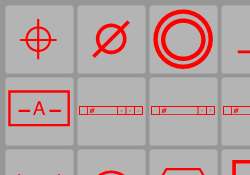
“We realized that if we were going to continue to grow and be successful, we had to do our best to streamline the processes that we had, and we did that by creating a value stream map of the project delivery from the point of award to project completion.”

“Around 2014, we embarked on a lean journey,” recalls Ed Gould, general project superintendent, Interstate Electrical.

New builds, ground-up restorations and BIM coordination are all hallmarks of the firm’s duties, along with fire alarm installation, testing and monitoring, arc flash hazard analysis, infrared testing, network data cabling, and process and building controls installations. “Our innovative vision is to use technology to support our operations and the people in the field, while increasing the value we provide to our customers.”įrom a value-add services standpoint, Interstate Electrical tackles everything from Fortune 500-level projects to fit-ups for startups, using design-build and design-assist services with an in-house team of professional engineers and electrical designers. “We want to be seen as ‘not your father’s electrical company,’” explains Bob Sanford, Interstate Electrical’s lead sales engineer. Founded in 1966 by Pat Alibrandi and currently led by his son Jim Alibrandi, Interstate aspires to be a different kind of electrical contracting company ─ one where individual talent and determination is encouraged and rewarded and one that is equally customer-centric. Interstate Electrical is a regional, family-owned, commercial electrical contractor with offices in all six New England states. Markups were made on physical drawings and presented problems: there were multiple copies, notes were hard to read and accuracy was not optimal.ĬAD detailers were used to create drawings for markups, resulting in a costly and time-consuming back and forth verification process that also mismanaged CAD time and use. Cut sheets faced a similar problem with no standardization options to accurately send information to the prefab team. Challenge Project information was on paper in non-scalable PDFs, and information flow and accuracy were hindered as drawings were marked and reprinted each time by hand and distributed via paper to project stakeholders.Įstimation was done using a combination of wheel-and-paper process, Microsoft Excel and other software, resulting in a slowed, bulky process that yielded costly errors and rework.Ĭhange orders were done with side-by-side paper comparison, taking valuable time and resources for item verification and quantities.Īs-built drawings could not be accurately scaled, leaving time-consuming manual verifications and room for error.
